(Di Rossella Mimmi, Emerson) – La richiesta di idrogeno è aumentata in modo esponenziale, ma l’idrogeno elementare esiste a malapena nell’atmosfera terrestre, costituendo circa lo 0,00005% in volume dell’aria atmosferica.
I processi industriali sono quindi la fonte principale per le forniture globali di idrogeno, prodotto in genere mediante steam reforming del metano (SMR) o autothermal reforming (ATR).
Sfortunatamente, entrambi questi processi producono idrogeno grigio perché generano notevoli emissioni di CO2 e di altro tipo.
Leggi anche: Scalare con successo la produzione di idrogeno verde lungo l’intera catena di valore.
Un metodo di produzione di recente introduzione è l’idrogeno blu, che utilizza gli stessi processi o processi simili alla produzione di idrogeno grigio, ma cattura e immagazzina la maggior parte, se non tutte, le emissioni di gas serra risultanti.
Questo metodo può utilizzare le apparecchiature e le tecnologie SMR o ATR esistenti per produrre volumi molto elevati di idrogeno, ma con emissioni di gas serra significativamente ridotte.
Esistono differenze e somiglianze tra SMR e ATR e ciascuno di essi presenta pro e contro, come descritto di seguito.
Produzione di idrogeno blu con SMR
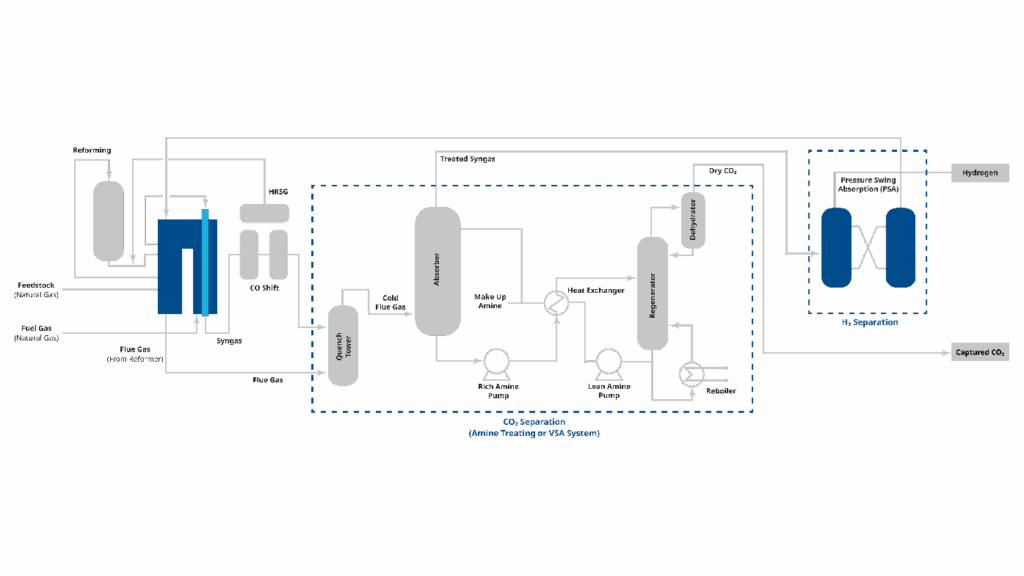
Il gas naturale viene desolforato e preriscaldato, quindi miscelato con vapore ad alta pressione e ulteriormente riscaldato in presenza di un catalizzatore all’interno di un reformer alimentato a gas combustibile.
Il calore e il catalizzatore decompongono il metano (CH4) e il vapore (H2O) per creare un gas di sintesi (syngas) composto da idrogeno, anidride carbonica (CO2) e monossido di carbonio (CO).
I convertitori di turno fanno reagire il CO e l’acqua (H2O) rimanenti in CO2 e idrogeno.
La miscela di syngas purificata entra quindi nell’assorbitore di ammina, dove il liquido di ammina in circolazione assorbe la CO2.
L’idrogeno lascia la parte superiore dell’assorbitore per essere ulteriormente purificato in un adsorbitore ad oscillazione di pressione (PSA), mentre l’ammina carica di CO2 viene riscaldata e depressurizzata nel rigeneratore di ammina per separare la CO2 dal liquido.
La CO2 viene quindi rilasciata e sfiatata, mentre l’ammina viene raffreddata e restituita all’assorbitore di ammina per trattare altro syngas.
Le unità di produzione SMR a idrogeno grigio non catturano l’anidride carbonica, ma si limitano a sfiatare i fumi e la produzione di anidride carbonica amminica nell’atmosfera.
Un’unità di idrogeno blu aggiunge un’apparecchiatura di recupero dell’anidride carbonica per catturare e infine immagazzinare la CO2 prodotta dall’SMR.
Queste fasi di processo aggiuntive aggiungono costi di capitale e di esercizio, ma consentono a un’unità SMR esistente di operare con un’impronta di carbonio molto ridotta.
I principali vantaggi degli SMR rispetto alle unità ATR sono le loro operazioni ben conosciute e la loro abbondante presenza in tutto il mondo.
Il costo aggiuntivo dell’aggiunta di un’unità di cattura del biossido di carbonio a un SMR è relativamente basso rispetto alla costruzione di un nuovo impianto.
Lo svantaggio di un SMR è che la cattura completa del carbonio è piuttosto difficile.
La CO2 relativamente concentrata e pulita che esce dall’unità di ammina è facile da catturare, ma la CO2 meno concentrata e impura associata ai gas di combustione non è così facilmente scrubbabile e recuperabile.
La conversione dei sistemi SMR alla produzione di idrogeno blu è relativamente semplice. La CO2 proveniente dall’unità amminica viene ulteriormente depurata, pressurizzata e liquefatta per essere trasferita a un impianto di stoccaggio del carbonio.
Se i gas di scarico sono convogliati verso l’unità amminica, come mostrato nella Figura 1, potrebbero essere necessarie ulteriori fasi di trattamento per pulire il gas.
La maggior parte degli impianti SMR convertiti per produrre idrogeno blu tendono a concentrarsi sull’anidride carbonica generata nella sezione amminica, mentre sfiatano i gas di scarico, poiché il loro recupero è molto più difficile e costoso.
Produzione di idrogeno blu con ATR
L’ATR è un processo più recente che si sta affermando nell’ambito della progettazione dell’idrogeno blu.
Utilizza molte delle stesse fasi dell’SMR, ma è più efficiente dal punto di vista dei consumi e crea un unico flusso di CO2 concentrato, anziché due come nel caso dell’SMR.
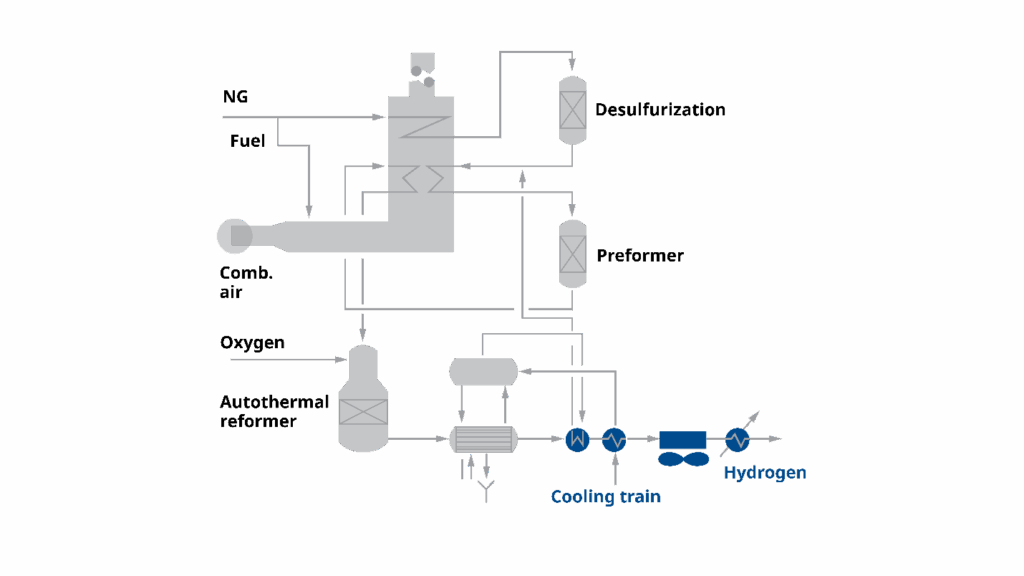
Il gas naturale viene desolforato e preriscaldato, quindi miscelato con vapore ad alta pressione e ulteriormente riscaldato in presenza di un catalizzatore. Questo gas viene poi bruciato con ossigeno puro per creare un syngas ad altissima temperatura.
La differenza tra ATR e SMR è che le fasi iniziali dell’ATR richiedono pochissimo combustibile, se non addirittura nulla, mentre la maggior parte dell’energia proviene dalla fase di iniezione dell’ossigeno.
Ciò riduce i requisiti energetici e genera un unico flusso di CO2 puro e concentrato, facilmente catturabile.
A valle del reformer autotermico, come illustrato nella Figura 2, i processi SMR e ATR sono essenzialmente gli stessi.
I convertitori di turno fanno reagire il CO e l’acqua rimanenti creando CO2 e idrogeno, mentre la sezione amminica assorbe la CO2 dal flusso di gas prima che l’idrogeno venga purificato nel PSA
Il principale vantaggio delle unità ATR è che sono più efficienti dell’SMR per la produzione di idrogeno blu e consentono di catturare una quantità di gas serra molto maggiore rispetto all’SMR.
Lo svantaggio dell’ATR è la necessità di una fonte di ossigeno o di un’unità di separazione dell’aria. Inoltre, esistono molti meno progetti di impianti ATR, quindi la tecnologia è meno matura e viene messa in produzione solo ora.
Tuttavia, l’ATR è una tecnologia promettente e probabilmente preferita per i progetti futuri destinati alla produzione di idrogeno blu, poiché è stata progettata specificamente per questo servizio. Esistono diversi impianti ATR in varie fasi di progettazione e costruzione in tutto il mondo.
Valvole, regolatori e valvole di sfiato nella produzione di idrogeno blu
Sia che si utilizzi la tecnologia SMR o ATR, il processo di idrogeno blu pone una serie di sfide alle valvole automatiche, ai regolatori e alle valvole di sicurezza che aiutano a controllare e proteggere il processo.
La presenza di idrogeno nel flusso di gas di sintesi caldo intorno ai reformer e nel prodotto finale crea sfide significative per le apparecchiature di controllo.
L’infragilimento da idrogeno può degradare l’integrità meccanica e le prestazioni delle valvole, con conseguente aumento delle emissioni e delle inefficienze.
Anche le alte pressioni e le temperature sono comuni e i vari componenti per il gas richiedono una gamma di materiali di costruzione adatti a ogni applicazione.
Le valvole di blocco manuali e automatiche devono includere i materiali di costruzione corretti, avere una classificazione di sicurezza antincendio certificata API 607 e possono richiedere la certificazione SIL 3 per le applicazioni di arresto (vedi foto sottostante).
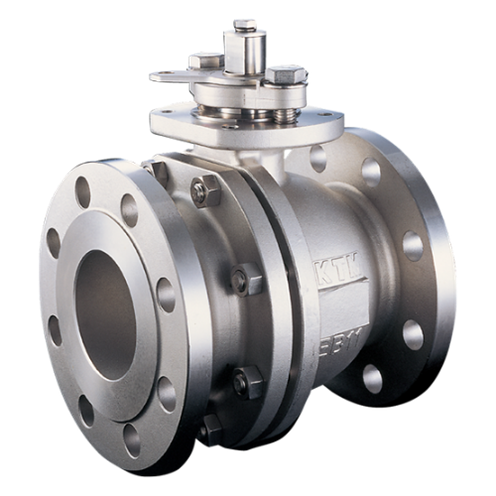
Le valvole a sfera selezionate devono avere sedi resistenti per le applicazioni a bassa temperatura e i materiali corretti per le applicazioni ad alta temperatura.
Devono inoltre possedere le certificazioni API e SIL richieste, offrire imballaggi a bassa emissione con carico in tensione e una varietà di stili di corpo, oltre ad avere una comprovata esperienza nel servizio ad alta pressione e idrogeno.
A seconda delle condizioni specifiche e delle dimensioni delle tubazioni, una valvola a sfera a doppio eccentrico o una valvola a farfalla a triplo offset con sede in metallo può essere un’alternativa alla valvola di isolamento.
Entrambe le valvole sono adatte a un’ampia gamma di temperature, pressioni e condizioni del fluido ed entrambe sono intrinsecamente resistenti al fuoco. Queste valvole sono descritte in dettaglio qui di seguito.
L’ampia gamma di materiali richiesti può essere un problema per la scelta del regolatore a causa della gamma limitata di opzioni.
Fortunatamente, alcuni modelli possono essere selezionati in acciaio inossidabile, Monel, Hastelloy o bronzo nichel-alluminio per fornire un controllo in un’ampia gamma di pressioni da 5 a 150 PSI.
Per questi processi sono spesso necessarie valvole di sicurezza ad alta capacità, che devono chiudere ermeticamente per evitare perdite di prodotto.
Inoltre, le valvole di sicurezza possono funzionare vicino ai loro valori di pressione di taratura, rendendo ancora più difficile ottenere e mantenere una tenuta ermetica.
Le valvole di sicurezza pilotate a tenuta migliorata funzionano bene in queste applicazioni. Questi tipi di valvole di sicurezza pilotate hanno una capacità molto elevata e i modelli più recenti consentono alla valvola di funzionare entro il 2% del suo setpoint con perdite minime.
Selezione della valvola di controllo per la cattura del carbonio
Sia che si utilizzi l’SMR o l’ATR, le fasi generali di lavorazione sono relativamente simili tra i due progetti di impianto una volta prodotto il syngas.
In entrambi i processi, la valvola di alimentazione dell’ammina magra è fondamentale per il corretto funzionamento.
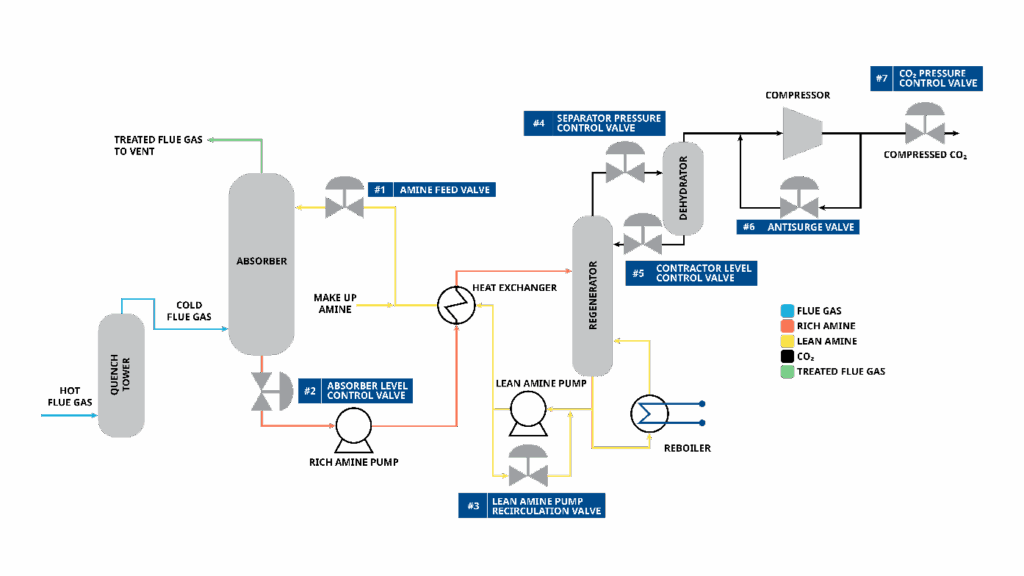
Per eliminare efficacemente la CO2 dal syngas, la valvola di alimentazione dell’ammina magra deve fornire un flusso costante di ammina alla parte superiore dell’assorbitore, nonostante l’elevata caduta di pressione e le condizioni di cavitazione.
La valvola migliore per questa applicazione sarà una valvola a sede singola in 316SS con lega 6 temprata, guarnizione anti-cavitazione e baderna potenziata.
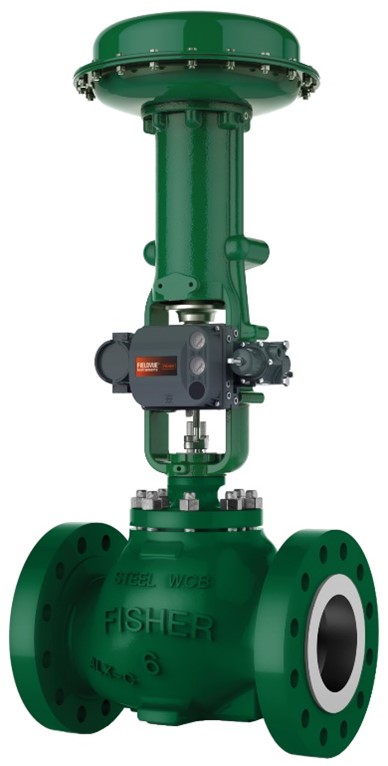
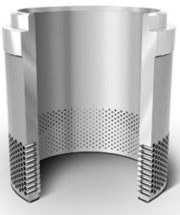
La valvola di alimentazione dell’ammina magra è soggetta a cavitazione e a un certo livello di corrosione. Una valvola di controllo in acciaio inox 316 (a sinistra) con finiture temprate anti-cavitazione (a destra) è una buona scelta per questa applicazione
Valvole di isolamento PSA
Le valvole intorno ai PSA sono soggette a condizioni di servizio molto impegnative.
Queste valvole sono sottoposte a cicli continui e devono mantenere perdite praticamente nulle e basse emissioni, garantendo al contempo le prestazioni di isolamento, nonostante le condizioni di alta pressione e vuoto, le temperature elevate e la presenza di materiali erosivi a letto di polvere.
Rispetto ad altri tipi di valvole automatiche, le valvole triplo eccentriche (Figura 6) offrono un ingombro minore e un peso inferiore, una migliore operatività, una riduzione delle emissioni fuggitive e una maggiore durata della valvola per questa difficile applicazione.
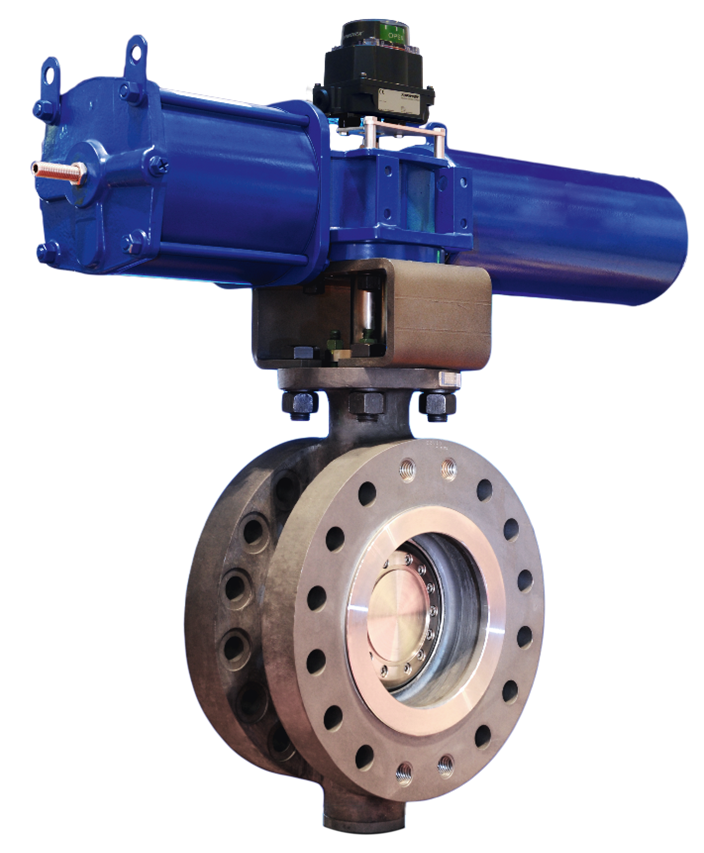
La valvola triplo eccentrica scelta per questo servizio usa la lega Stellite™ 21 come standard per il rivestimento della sede del corpo valvola, per ottenere una maggiore resistenza a graffiatura, abrasione, erosione e corrosione.
Questa caratteristica, unita a un anello di tenuta solido, a componenti dell’albero rinforzati e a un premistoppa caricato in tensione, rende questo tipo di valvola la scelta preferita per questa applicazione, in quanto garantisce perdite sostanzialmente nulle, nonostante le condizioni di servizio molto difficili.
Un’altra opzione per le valvole di isolamento PSA è la valvola a sfera a doppio eccentrico (Figura 7).
Utilizza un design a doppio offset per creare una tenuta a perdita zero che funziona indipendentemente dalla pressione applicata.
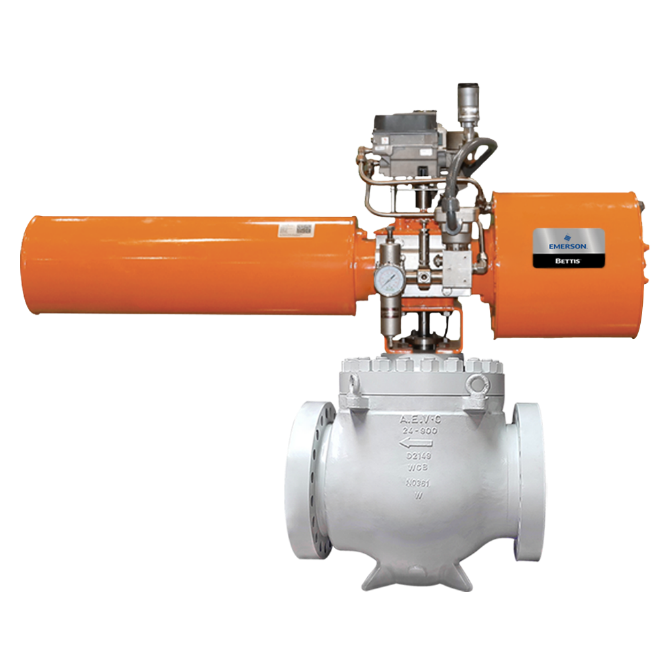
Un effetto di cammamento allontana la sfera C dalla sede durante la corsa di apertura per ridurre al minimo l’usura in presenza di abrasivi.
La combinazione di sedi metalliche fisse, tenuta meccanica indipendente dalla pressione di processo, bassa usura e design a basse emissioni funziona bene anche in queste condizioni difficili.
Attuatori remoti per valvole per condotte
Alcune valvole automatiche possono essere installate in luoghi in cui non è disponibile l’aria.
In queste applicazioni, sono necessari attuatori elettrici o attuatori azionati dalla pressione della tubazione (Figura 8).
I requisiti di coppia più bassi possono essere soddisfatti con i moderni attuatori elettrici, con o senza funzione di molla di arresto.
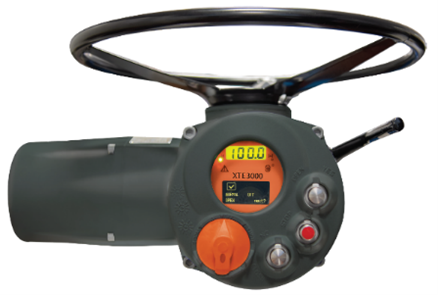
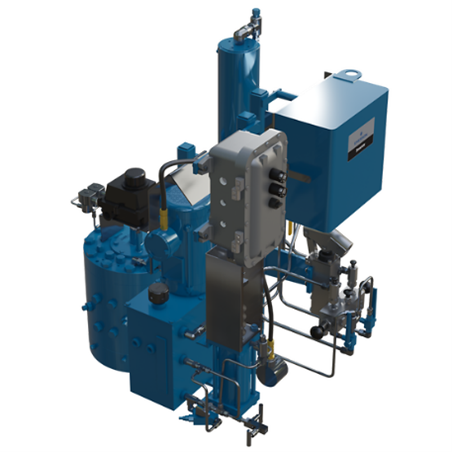
Le applicazioni per condotte che richiedono una coppia elevata o che coinvolgono più valvole possono utilizzare sistemi di attuazione idraulica a emissioni zero.
Queste unità utilizzano la pressione della conduttura per azionare le valvole idrauliche e il gas della conduttura viene iniettato di nuovo nella tubatura a fine corsa, quindi non ci sono emissioni.
Le unità di processo per l’idrogeno sono in funzione da decenni, ma non nella scala prevista per il futuro.
I principali fornitori di automazione hanno una vasta esperienza con queste unità e gran parte della loro competenza è applicabile ai nuovi processi descritti in questo articolo, in particolare la cattura e il trasporto del carbonio necessari per convertire l’idrogeno grigio in idrogeno blu.
Quando si progettano i sistemi necessari per convertire l’idrogeno grigio in idrogeno blu, le società operative farebbero bene a rivolgersi a un fornitore che abbia una vasta esperienza nella gestione dell’idrogeno e che sia in grado di applicare questa esperienza su scala mondiale.
Per ulteriori informazioni consultate il sito https://www.emerson.com/it-it/automation/valves/h2-solutions