E’ per noi un grandissimo piacere raccontarvi in questo nuovo speciale la nostra recente visita al Laboratorio H2 IIS SIDER di Castel San Giovanni, in provincia di Piacenza, un centro di eccellenza specializzato in prove meccaniche su materiali in ambiente idrogeno gassoso ad alta pressione, fino a 1.500 bar.
Attraverso le parole dell’Amministratore Delegato, la Dott.ssa Lucia Soprana, e del Direttore Tecnico, il Dr. PhD. Marco Palombo, ai quali esprimiamo gratitudine per la loro disponibilità e cordiale accoglienza, vi condurremo passo dopo passo nel laboratorio, raccontandone la storia, le attività, i servizi e le soluzioni tecnologiche che poche altre strutture in Europa possono offrire.
A Voi tutti buona lettura!
H2 IIS Sider
Tutto inizia, come sempre, da un’idea.
L’idea che due entità storiche, l’Istituto Italiano della Saldatura (IIS) e Sider Test, uniscano le proprie conoscenze e i risultati di anni di collaborazione per fondare una realtà altamente tecnologica e specializzata, capace di affrontare con successo le sfide energetiche del futuro.
Ed è proprio così che nel Giugno 2022 viene costituita, in una delle tre sedi piacentine di Sider Test, H2 IIS SIDER.
Soprana: “L’investimento alla base è stato molto importante. Abbiamo accettato con entusiasmo il progetto anche per un discorso di “guardare avanti”, non solo a un mercato che sino ad allora è stato di nostro riferimento, quello dell’Oil&Gas, ma verso un settore energetico nuovo, quello dell’idrogeno, in fase di evoluzione”.
Palombo: “La prima fase del progetto ha richiesto tempo per la fornitura delle attrezzature, molto avanzate tecnologicamente, e poiché abbiamo investito molto nella progettazione e nella sicurezza dell’impianto che lavora con idrogeno e gas inerti fino a 1500 bar di pressione”.
Dal giorno della fondazione, sia l’IIS che Sider Test supportano il team garantendo ogni tipo di servizio necessario, dall’assistenza tecnica e commerciale alla lavorazione e fornitura dei provini.
“Sfruttando le competenze delle due società fondatrici, che dispongono anche di tantissime facilities sul territorio, possiamo offrire ai clienti servizi sicuri, precisi ed affidabili”.
Le attività del Laboratorio
Partiamo subito sottolineando che H2 IIS SIDER è una realtà dinamica.
Ad oggi, quello svolto dal team è un lavoro assai diversificato che spazia dalla consulenza alla stesura di specifiche campagne di prova, che sono utili alla caratterizzazione di un prodotto per definirne la compatibilità con l’idrogeno, fino allo svolgimento di prove specifiche su richiesta.
L’obiettivo finale del laboratorio è quello di offrire ai propri clienti consigli pratici di problem-solving, utilizzabili nell’immediato, con l’accuratezza e la precisione della ricerca scientifica.
Palombo: “Per lavorare con l’idrogeno occorrono competenza e un approccio scientifico. Siccome i tipi di test sono diversi e complessi, di conseguenzaanche le tecnologie necessarie per la loro esecuzione richiedono molta accuratezza e personale specializzato”.
“Svolgiamo per lo più test di tipo meccanico utili alla caratterizzazione delle proprietà di un materiale, di una saldatura o di un componente in ambiente idrogeno gassoso”.
“Possiamo condurre prove statiche, cicliche, a fatica e per la propagazione di difetti, meccanica della frattura, prove di tenuta, prove customizzate, ma anche prove a lungo termine o di invecchiamento; queste ultime vengono utilizzate, oltre che nel campo dei metalli, anche per sigillanti e materiali polimerici, dove si studia il confronto tra le caratteristiche del materiale, misurate prima e dopo l’esposizione all’ambiente idrogeno”.
Tra i materiali oggetto di studio vi sono gli acciai inossidabili e al carbonio e le leghe di nichel, usati per il trasporto, stoccaggio e distribuzione dell’idrogeno, nonché sigillanti e guarnizioni.
Durante il giorno della nostra visita, ad esempio, si stava svolgendo un test a 1.000 bar per esaminare gli effetti di una stessa prova su materiali completamente differenti, come l’adesivo e il metallo.
Le sfide dell’idrogeno
Le principali sfide che il team deve affrontare quotidianamente sono legate all’affidabilità dei risultati e alla difficoltà nell’ottenere una misura accurata all’interno di un autoclave a 1.500 bar di pressione.
Data la complessità dei test, che interessano geometrie complesse e richiedono in certi casi tempi di esecuzione molto lunghi, per H2 IIS SIDER è fondamentale ottimizzare al meglio le prove, per essere poi certi del risultato ottenuto.
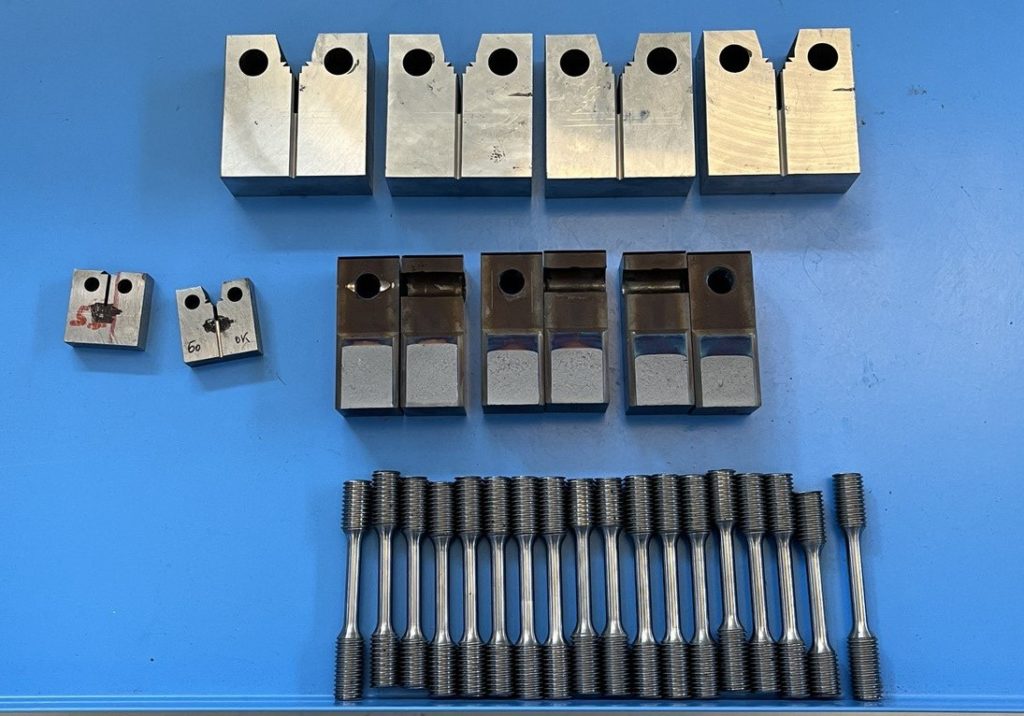
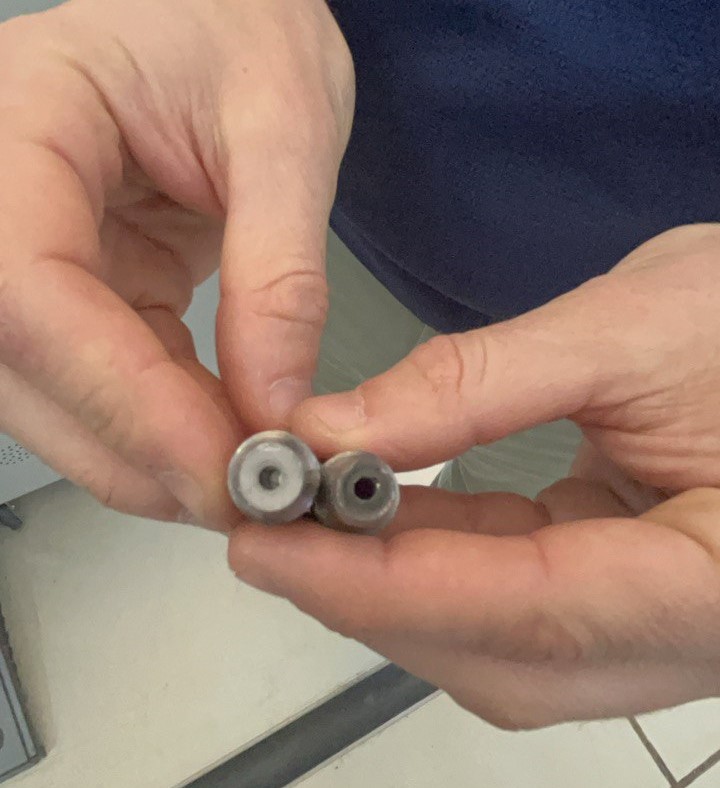
Palombo: “Tra i nostri clienti ci sono persone molto preparate ed esigenti, con una conoscenza molto ampia dell’interazione tra idrogeno e materiali”.
“Per i metalli la durata delle prove a lungo termine varia da 1.000 a 5.000 ore a seconda del tipo di materiale, quindi da 40 giorni a 7 mesi”.
“Le altre prove statiche, meccaniche, prove di meccanica della frattura, etc., possono richiedere invece qualche ora. A prova! Ci sono poi prove di fatica che possono durare una settimana o più”.
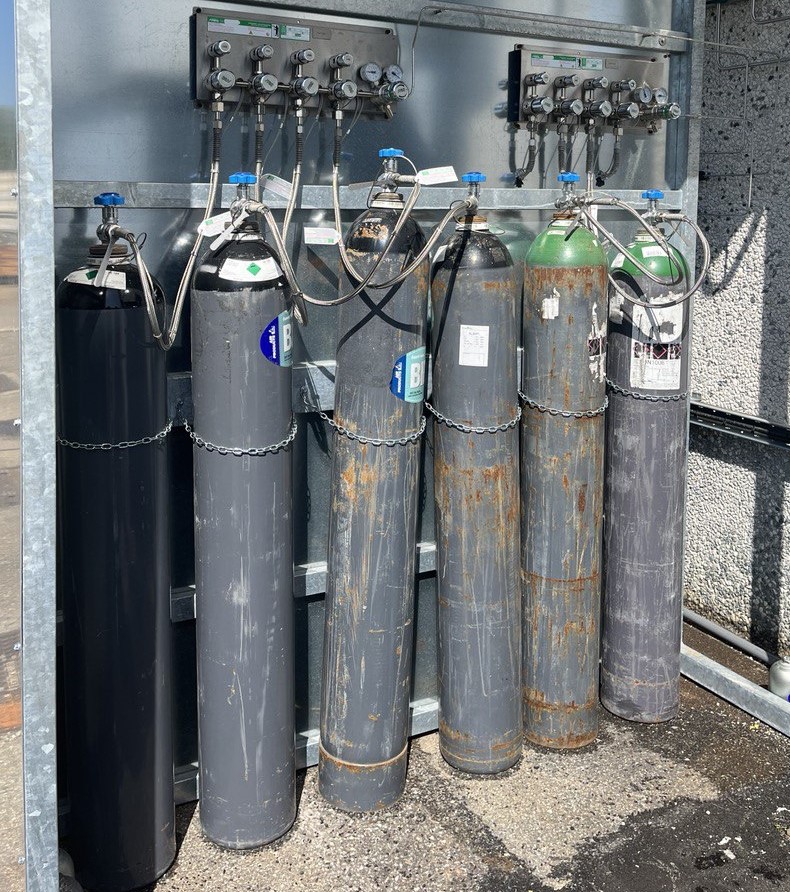
L’idrogeno viene fornito al laboratorio in quattro bombole standard, sistemate su un rack all’esterno dell’edificio. Nel box ci sono anche quattro bombole di argon e quattro di azoto, per un totale di dodici bombole.
Dopo aver collegato le bombole all’impianto, il team effettua diversi cicli di lavaggio per assicurarsi che l’atmosfera all’interno delle autoclavi raggiunga una purezza quanto più possibile vicina a quella certificata per le bombole, che in questo caso è di grado 6.
“A seconda della pressione di lavoro occorre da mezzora a un’ora e mezza per portare l’autoclave in pressione. Questo consuma tantissimo tempo e quindi abbiamo una capacità produttiva limitata”.
Guardare avanti
Se da una parte ci si augura che il mercato dell’idrogeno cresca sempre di più nei prossimi anni, dall’altra persiste ancora una sensazione di incertezza, in particolare per quanto riguarda l’ambito normativo.
“Molti clienti ci contattano un po’ sconcertati perché ora il mercato chiede prodotti certificati H2 e non trovano riferimenti applicabili ai loro prodotti”.
“I codici disponibili oggi sono parzialmente allineati con la velocità di crescita e di sviluppo dell’industria. I fornitori dei top-player attivi nella produzione o nel trasporto dell’idrogeno, hanno difficoltà a garantire l’idoneità dei loro prodotti al Hydrogen Service perché non trovano un quadro normativo adeguato. E quindi chiedono aiuto anche a noi”.
La speranza, secondo H2 IIS SIDER, è che presto siano definiti codici in grado di fornire indicazioni e linee guida chiare e percorribili, sia tecnicamente che economicamente. Ma non solo.
Soprana: “Ci auguriamo che anche nelle specifiche di progetto vengano inserite le norme, i tipi di test richiesti per poi poter vendere quei tipi di prodotti altrimenti i produttori non sapranno quali test eseguire per soddisfare i requisiti del cliente finale che spesso, a sua volta, non è a conoscenza delle prove da richiedere”.
Tra i clienti partner vi sono imprese di trasporto gas, operanti a pressioni ridotte (tra 70 -100 bar), e di stoccaggio, che necessitano di materiali e spessori variabili, da pochi millimetri fino a diversi centimetri, con pressioni che vanno dai 200 ai 1200 bar.
Spazio anche a collaborazioni con il settore della Ricerca e Sviluppo.
Nel Laboratorio
La sicurezza
Prima di soffermarci sulle singole attrezzature presenti nel Laboratorio, vogliamo parlarvi dell’impianto di sicurezza.
Come menzionato in precedenza, la sua progettazione ha richiesto un tempo considerevole: all’incirca due mesi per l’installazione iniziale, seguiti da numerosi test e simulazioni per situazioni d’emergenza.
La procedura di sicurezza che precede i test si basa integralmente sul principio del “doppio controllo”.
Una volta messa in posizione la macchina di prova, la porta dell’autoclave viene chiusa elettronicamente.
Successivamente, l’attivazione della valvola a farfalla, situata accanto alla porta, insieme al sistema di controllo della ventilazione (foto in basso a sinistra), autorizza l’operatività dell’impianto centrale, la quale deve tuttavia essere sempre approvata personalmente dal team.
Ognuna delle stanze in cui sono installati gli autoclavi è dotata di appositi sensori per il rilevamento di eventuali perdite di idrogeno.
Se il sensore centrale del laboratorio rileva fughe di idrogeno l’intero sistema si spegne automaticamente e pertanto non è possibile avviare i test (vuol dire che gli altri hanno fallito).
I sensori sono gestiti da un sistema che fornisce un valore in % del limite di esplosività inferiore (foto in basso a destra), ovvero il valore minimo di concentrazione di idrogeno nell’aria in grado di produrre esplosione.
Il valore minimo calcolato è di 4.4%.
A seconda del livello rilevato si avviano una serie di azioni.
Per prima cosa si bloccano tutte le rampe di pressurizzazione, si svuotano le autoclavi, si blocca l’alimentazione della pompa, e, in caso di emergenza estrema, si taglia la corrente generale aprendo in automatico le valvole a soffitto.
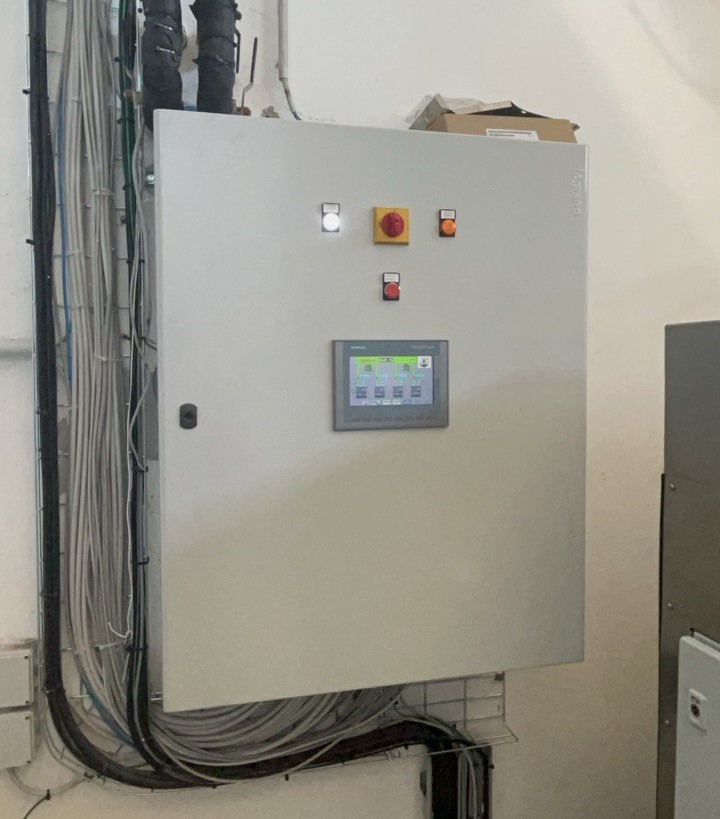
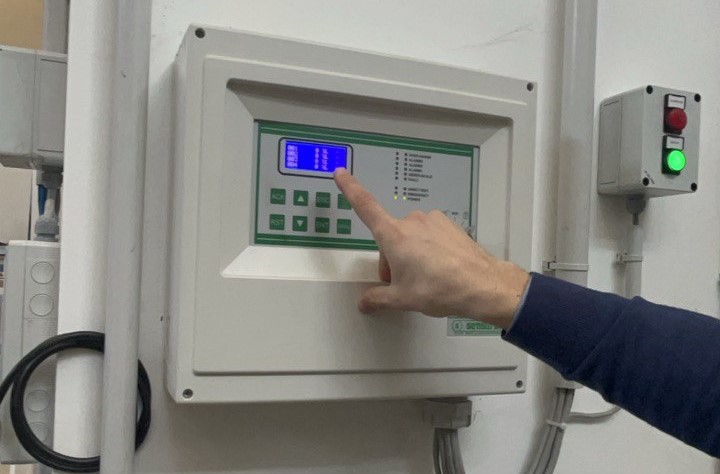
Le attrezzature e i test
Dopo la sicurezza veniamo ora al resto dell’impianto.
La definizione completa del progetto ha richiesto qualche mese più un anno di studio pregresso e circa nove mesi di modifiche continue.
Il laboratorio dispone di tre autoclavi contenenti le macchine di prova, fornite da un partner storico di IIS e Sidertest, e personalizzate dal team di H2 IIS SIDER per poter incrementare ancora di più le loro prestazioni al top di gamma, soprattutto in termini di precisione.
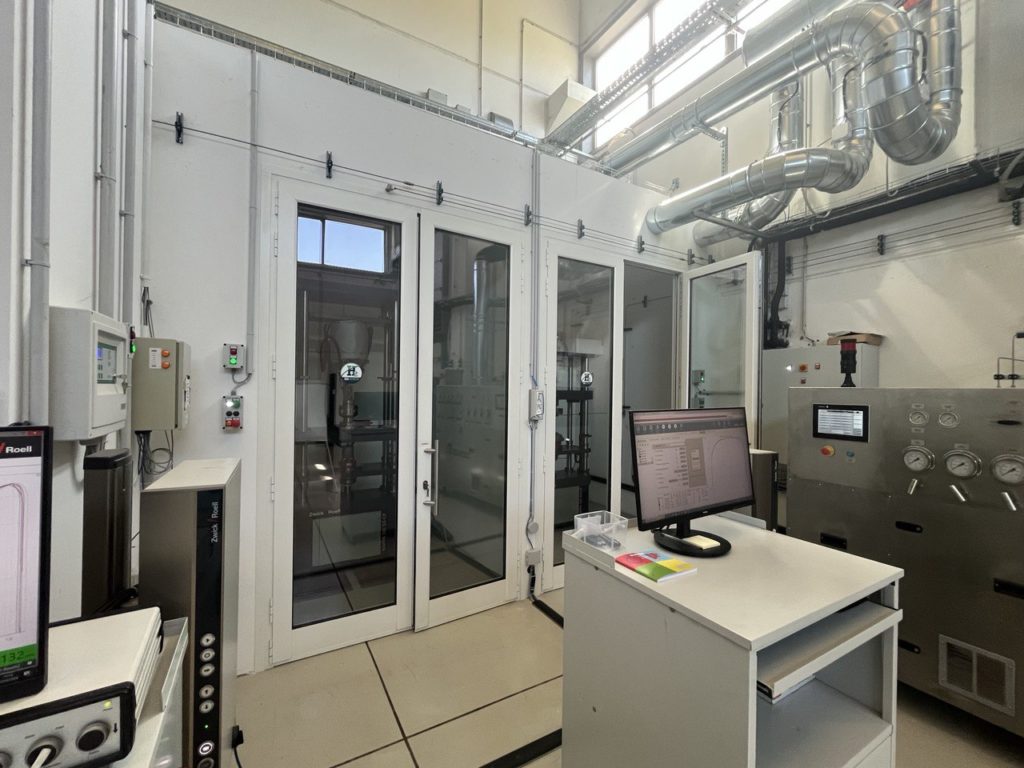
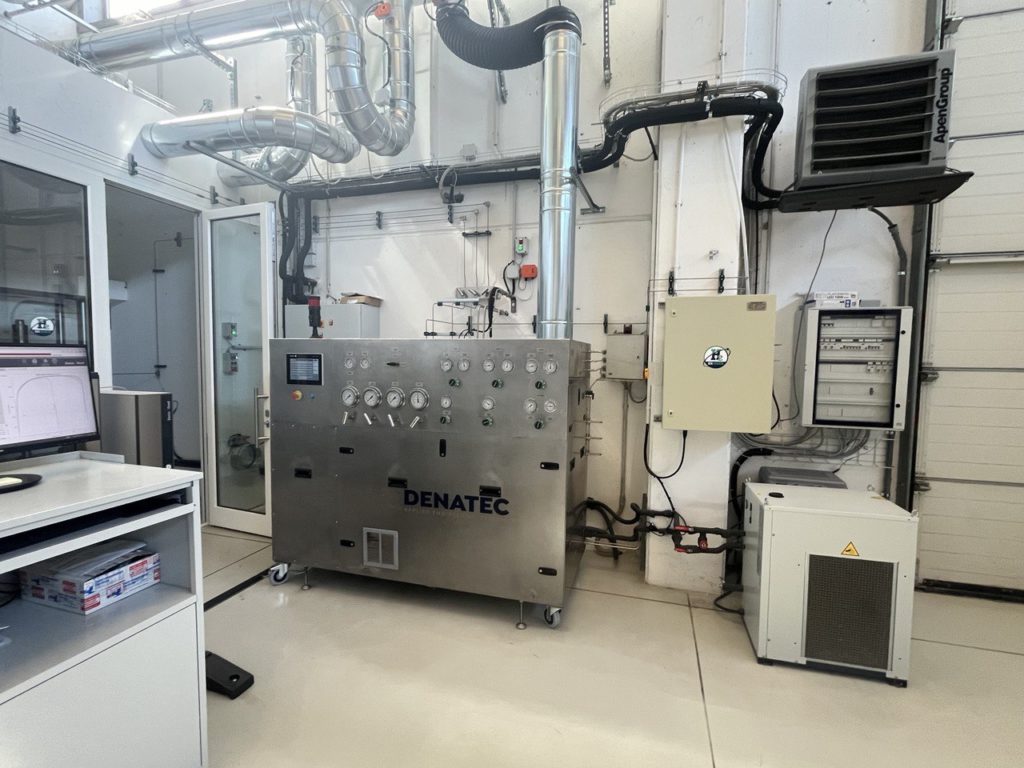
Le tre autoclavi sono dedicate a:
- Prove statiche (meccanica della frattura o prove di trazione a velocità di deformazione lenta o slow strain rate);
- Prove cicliche (a fatica o determinazione del rateo di crescita delle cricche da fatica);
- Prove a lungo termine;
- Prove su provini hollow o tubolari.
Autoclave per prove a lungo termine – K1H
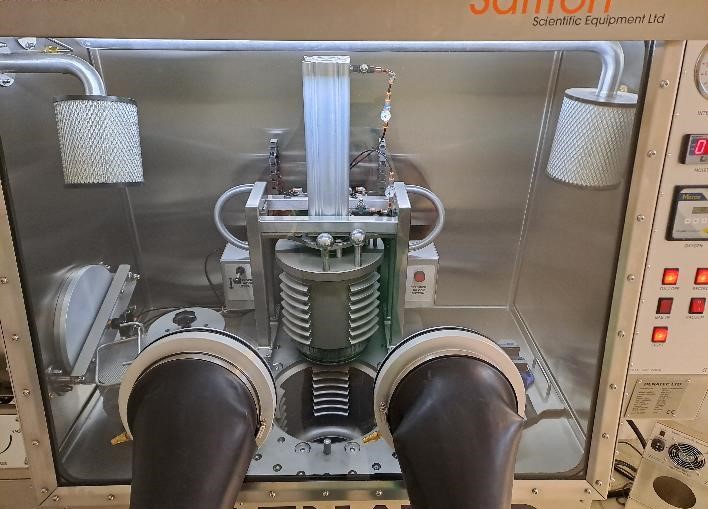
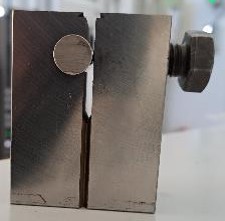
Questa autoclave da 6 litri consente il mantenimento delle condizioni in ambiente idrogeno ad una pressione regolabile fino a un massimo di 1.500 bar.
L’ambiente in pressione di idrogeno viene mantenuto per tutta la durata della prova.
All’interno sono svolte prove di meccanica della frattura (per 1000 o 5000 ore) per determinare il valore di soglia o del fattore di intensificazione delle tensioni, K, in condizioni di propagazione di un difetto.
I provini hanno una geometria particolare (bolt-load CT) che permette l’applicazione di un carico iniziale (scostamento costante) tramite il serraggio di una vite.
Questi vengono manipolati (precaricati avvitando la vite) in ambiente inerte in modo da evitare la passivazione del fronte di propagazione della cricca.
Dopo il periodo di esposizione, i campioni sono analizzati tramite microscopio elettronico a scansione per controllare l’eventuale propagazione del difetto e il suo aspetto.
Prove statiche – SSRT / J1H
Il laboratorio è dotato di due macchine di prova con una capacità di carico fino a 100 kN: una presenta un’autoclave da 2 LT, l’altra di raccordi specifici è caratterizzata di un’attrezzatura cava per campioni cavi o tubolari (hollow).
Su provini cilindrici (lisci o intagliati) o tubolari e cavi sono eseguite prove a lenta velocità di deformazione (Slow Strain Rate Test) e prove meccaniche della frattura per determinare la tenacità del materiale misurando l’integrale J (grandezza convertibile nel K sopra citato).
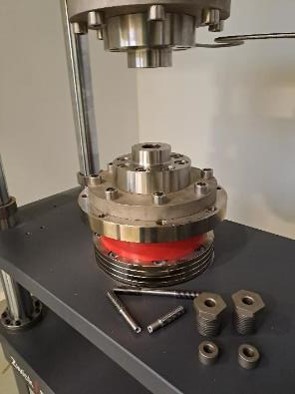
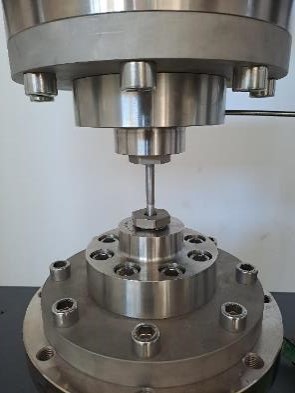
Le prove SSRT su provini intagliati vengono tipicamente eseguite a bassa velocità sia in ambiente inerte che in idrogeno per verificare l’effetto di infragilimento di quest’ultimo sul NTS (Notch Tensile Strenght).
La macchina dedicata ai test su provini hollow presenta un sistema particolare che permette di allineare in modo fine la catena meccanica che tira il provino, in modo che sia perfettamente allineato.
Il provino viene montato con dei semplici raccordi filettati con un tipo di connessione che trasmette il gas dalla linea attraverso il provino stesso, definita “metallo su metallo”.
Dopo aver eseguito i cicli di lavaggio e mandato in pressione la macchina, il test ha inizio.
In foto si può vedere la differenza del test eseguito a 1.500 bar con l’azoto, il provino è più opaco e deformato, e con l’idrogeno, più fragile e con una rottura più netta.
Le caratteristiche meccaniche sono le stesse (l’idrogeno riduce la duttilità del materiale).
Prove cicliche a fatica– S-N / ε-N / FCGR
Le facilities a disposizione del laboratorio permettono di determinare curve di fatica (S-N e ε-N) e determinare il rateo di un difetto di fatica (Fatigue Crack Growth Rate, FCGR o da/dN) in ambiente idrogeno fino a 1.500 bar.
Queste prove cicliche (con frequenze di sollecitazione fino a 1 Hz) sono condotte sia su provini standard o intagliati che cavi o tubolari.
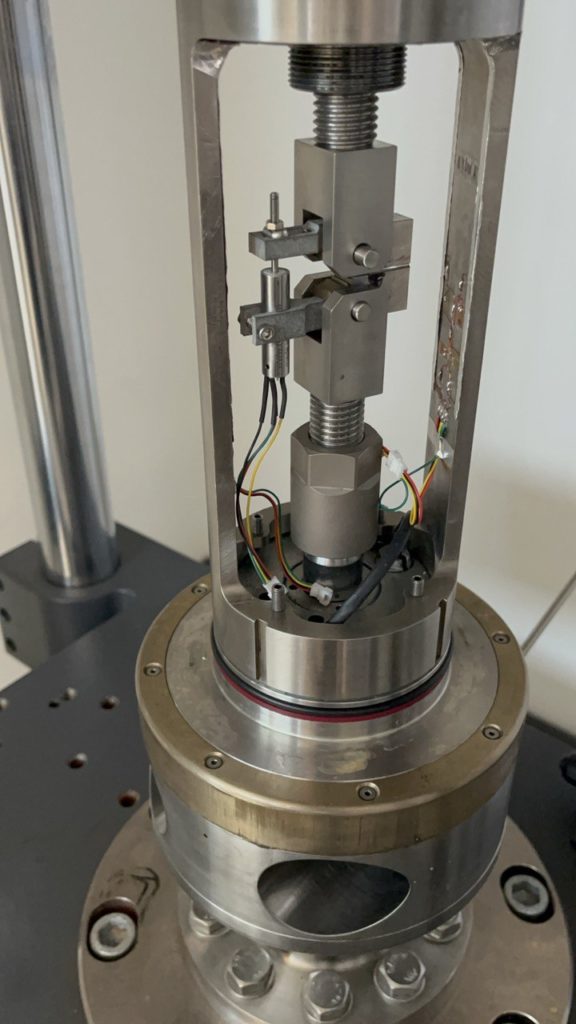
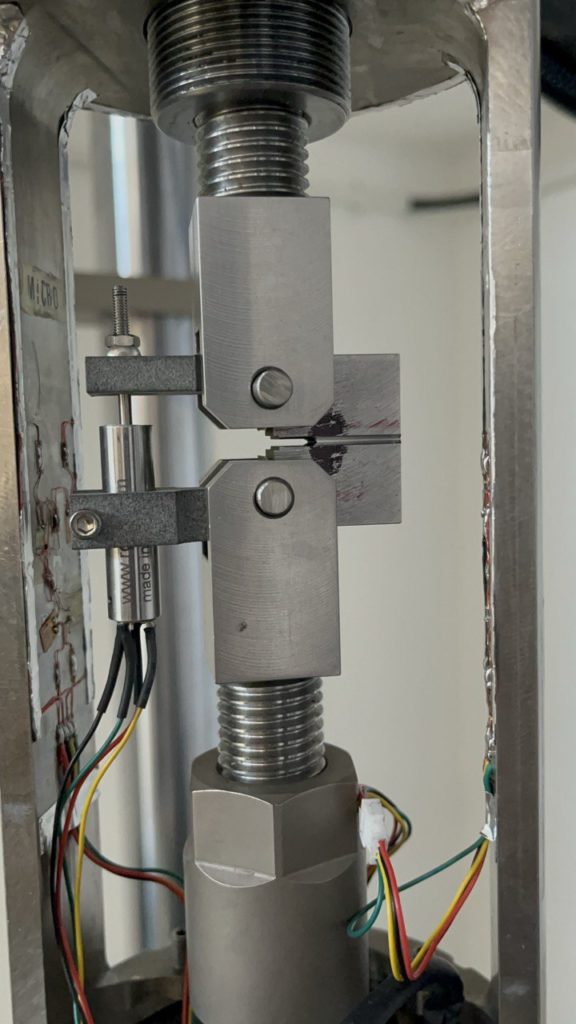
La strumentazione utilizzata per questi test è molto complessa e delicata e richiede costanti aggiornamenti e manutenzione dal team.
Questi includono, per esempio, l’utilizzo e l’installazione di sensori e componentistica sofisticata e costosa per monitorare con maggiore accuratezza e affidabilità i parametri di una prova durante il suo svolgimento.
Per maggiori informazioni su H2 IIS SIDER visitate il sito ufficiale al seguente Link.
Hydrogen-news.it vi invita alla terza edizione della HYDROGEN EXPO, a Piacenza dall’11 al 13 Settembre 2024.